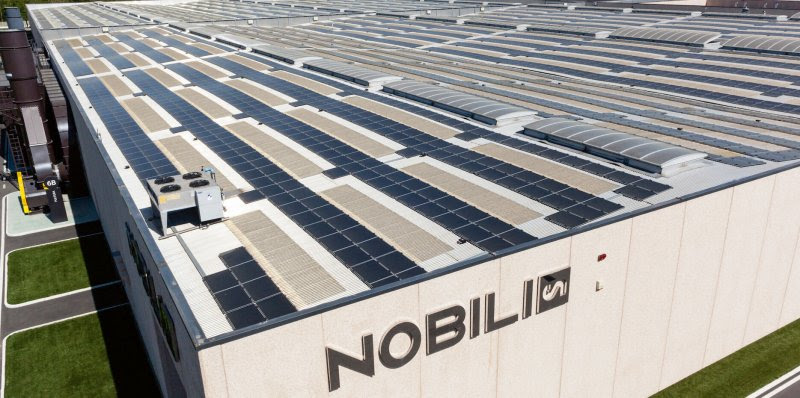
L’azienda piemontese leader in Europa grazie ai nuovi stabilimenti di Suno (NO)
Nuovi stabilimenti da 50.000 mq che si aggiungono ai precedenti 100.000 e trasformano la sede di Suno, in provincia di Novara, in uno dei più grandi e avanzati poli europei per la produzione di rubinetti: è il nuovo traguardo raggiunto da Nobili.
La struttura, composta da due edifici, verrà inaugurata ufficialmente nella primavera del 2022 ed è destinata a incrementare un fatturato che nel 2020 ha toccato quota 76,5 milioni di euro (+4% sul 2019) con 3,5 milioni di prodotti venduti. Per il primo produttore italiano del settore si tratta di una scommessa vinta, che consentirà la riconfigurazione degli stabilimenti, con il potenziamento dei reparti dedicati allo stampaggio delle materie plastiche e all’assemblaggio delle cartucce di miscelazione, l’aggiunta di 2 nuovi impianti galvanici per la cromatura e di un ulteriore reparto di stampaggio delle leghe metalliche.
Nel complesso, su una superficie di 150.000 metri quadri, il nuovo layout è pensato per supportare un processo di crescita costante e offrire al mercato uno standard qualitativo estremamente elevato. Con una peculiarità: Nobili è infatti l’unica azienda in Europa a mantenere il 100% del ciclo di produzione della rubinetteria all’interno dei propri stabilimenti. È inoltre la sola realtà italiana che disegna, progetta e realizza autonomamente sia i rubinetti che le cartucce di miscelazione.
In pratica 10 aziende in una: dalla tornitura all’iniezione dell’ottone fuso per bassa pressione; dallo stampaggio delle componenti plastiche – con 18 presse e oltre 15 milioni di componenti realizzati ogni anno – alla cromatura e poi lucidatura, lavorazioni laser, confezione, stoccaggio, gestione dei ricambi. Sono ben 452 i centri di lavoro dislocati nei diversi stabilimenti, 8.000 km la lunghezza delle barre di ottone lavorate ogni anno.
Grande attenzione all’efficienza energetica e al riciclaggio di ogni componente delle lavorazioni. Il truciolo di ottone, ad esempio, viene purificato dal lubrificante utilizzato nella fase di tornitura per essere nuovamente trasformato in barra. Lo stesso lubrificante viene recuperato e immesso nuovamente nei circuiti di utilizzo. Anche i due impianti di cromatura sono interamente a ciclo acque chiuso, con un recupero del 100% dell’acqua di scarto, poi utilizzata per il raffreddamento delle macchine. Gli stabilimenti sono classificati come «Zero Emission Company» grazie a un impianto fotovoltaico da da 1 MW, composto da 9.000 pannelli in grado di assicurare autonomia energetica e di garantire sofisticate soluzioni per la tutela dell’ambiente. Anche il packaging è ecosostenibile, con cartone certificato FSC, vernici naturali a base d’acqua e collanti di origine vegetale.
Condividi l'articolo
Scegli su quale Social Network vuoi condividere